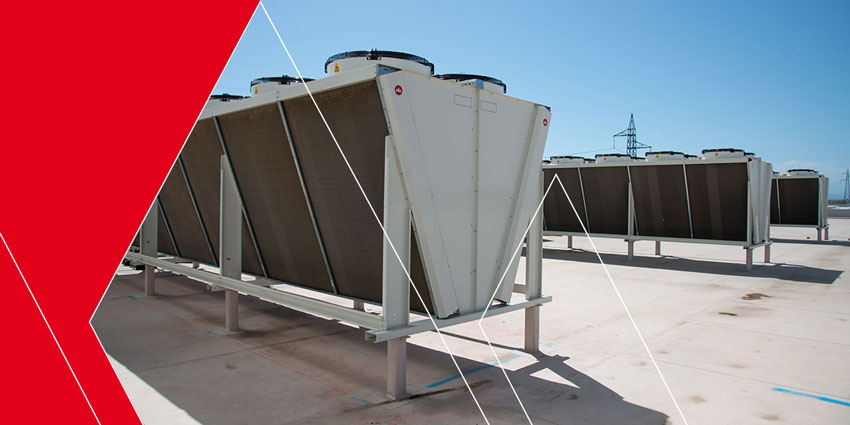
Piedmont, Italy
CO₂ hypercritical plant for industrial refrigeration
A refrigeration plant with low running costs to guarantee the cold cycle in one of Italy's largest Distribution Centres. The area in question is an extension of the plant and covers 13,000 m².
Storage description
Our customer Arneg built three large compressor refrigerating units for the plant, which supply the storage areas and food loading bays, ensuring the cold cycle. The choice of a hypercritical CO₂ system allowed significant annual energy savings due to the high efficiency of the cooling cycle and the low cost of CO₂ used as a coolant. In addition, the refrigeration units recover some of the heat produced during high compression to obtain domestic hot water and feed the office heating system.
Storage informations
To cover the future expansion of the plant, the three units develop a total cooling capacity of 1,850 kW. The transfer of heat is entrusted to three large OSTRO gas coolers with a condensing capacity of 3 MW.
Installed products
3 OSTRO gas coolers and 28 ventilated evaporators.
The imposing OSTRO “V” gas coolers were manufactured with all circuits in stainless steel to withstand the high pressures involved (PS 120 Bar). A special feature of the OSTRO units is the large heat exchange surface area, in relation to the size of the machines.
Advantage obtained
A great energy saving – only 35 Kwh/m³ per year – due to the efficiency of the hypercritical cycle and a help to the environment due to the use of CO₂ as a coolant fluid. Carbon dioxide is in fact a neutral gas and also very economical.
Refrigeration technology has made great strides in recent years and hypercritical systems are at the forefront of this revolution. These advanced systems offer significant advantages over traditional refrigeration methods and are increasingly being adopted by the most advanced companies. In fact, hypercritical systems offer not only a low environmental impact, but also better energy efficiency, reduced operating costs and increased safety levels.
The word to the costumer
“Stefani’s Ostro units are excellent gas coolers. Together with our control units, they allowed us to build a plant that fully met our customer’s expectations.”
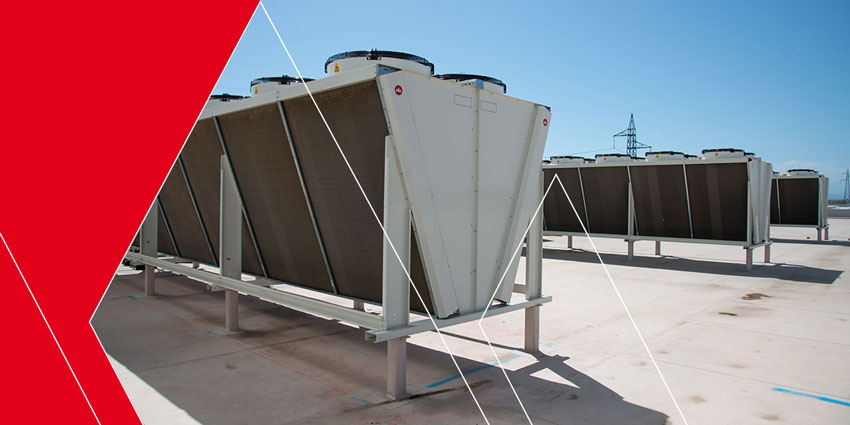
Piedmont, Italy
CO₂ hypercritical plant for industrial refrigeration
A refrigeration plant with low running costs to guarantee the cold cycle in one of Italy's largest Distribution Centres. The area in question is an extension of the plant and covers 13,000 m².
Storage description
Our customer Arneg built three large compressor refrigerating units for the plant, which supply the storage areas and food loading bays, ensuring the cold cycle. The choice of a hypercritical CO₂ system allowed significant annual energy savings due to the high efficiency of the cooling cycle and the low cost of CO₂ used as a coolant. In addition, the refrigeration units recover some of the heat produced during high compression to obtain domestic hot water and feed the office heating system.
Storage informations
To cover the future expansion of the plant, the three units develop a total cooling capacity of 1,850 kW. The transfer of heat is entrusted to three large OSTRO gas coolers with a condensing capacity of 3 MW.
Installed products
3 OSTRO gas coolers and 28 ventilated evaporators.
The imposing OSTRO “V” gas coolers were manufactured with all circuits in stainless steel to withstand the high pressures involved (PS 120 Bar). A special feature of the OSTRO units is the large heat exchange surface area, in relation to the size of the machines.
Advantage obtained
A great energy saving – only 35 Kwh/m³ per year – due to the efficiency of the hypercritical cycle and a help to the environment due to the use of CO₂ as a coolant fluid. Carbon dioxide is in fact a neutral gas and also very economical.
Refrigeration technology has made great strides in recent years and hypercritical systems are at the forefront of this revolution. These advanced systems offer significant advantages over traditional refrigeration methods and are increasingly being adopted by the most advanced companies. In fact, hypercritical systems offer not only a low environmental impact, but also better energy efficiency, reduced operating costs and increased safety levels.
The word to the costumer
“Stefani’s Ostro units are excellent gas coolers. Together with our control units, they allowed us to build a plant that fully met our customer’s expectations.”