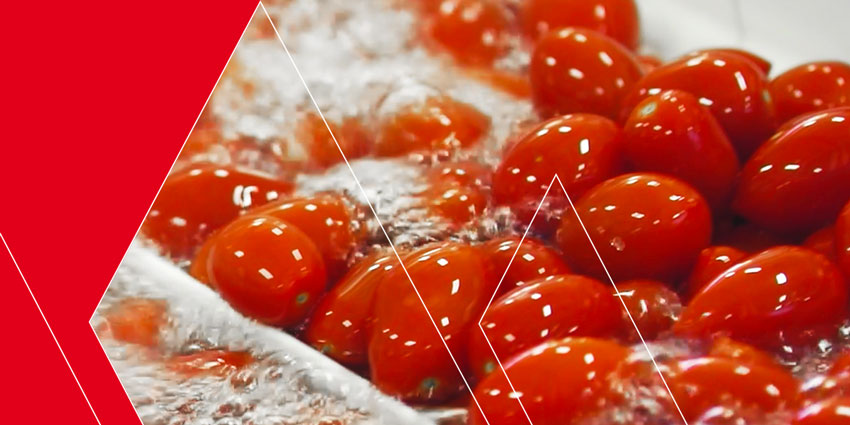
Emilia Romagna, Italy
Process cooling for a tomato processing plant
The end customer, one of Italy’s largest agri-food brands specialising in tomato processing, needs to cool the water from the tomato pulp pasteurisation process immediately after bottling in glass jars.
Storage description
This large plant is located near Cremona in the fertile Po Valley and includes all stages of tomato processing, from harvesting to bottling. The cooling of the pasteurisation process takes place in three consecutive phases: from 90 to 50°C, from 50 to 20°C and from 20 to 7°C. The technical solution – designed and implemented by Frigosystem and Termoidraulica Busi – is to include two powerful dry coolers, a remote condenser and a chiller in the cooling process. Stefani dry coolers operate in ‘free cooling’ in the first two phases, without the need for a chiller. In the last phase, however, the chiller comes into operation, disposing of the heat through the powerful Stefani remote condenser.
Storage informations
The plant produces 60,000 jars of tomato pulp per hour.
The cooling capacity used in process cooling is 3.0 MW in free cooling and 1.5 MW with the chiller.
Thanks to free cooling, the solution allows a 30% saving in electricity consumption.
Installed products
In the two free cooling phases: OSTRO dry coolers
A large exchange surface, in consideration of the size of the machines, and extremely powerful fans allow high-performance free cooling of the system.
In the cooling phase with the chiller: OSTRO remote condenser
The OSTRO XL series uses low refrigerant charge technology: less than 350 kg of gas for a 1500 kW condenser at DT 10K.
Advantage obtained
Thanks to the collaboration with our customer Frigosystem and Termoidraulica Busi, the end customer obtained a low energy solution, which also allows him to reduce water consumption. The OSTRO units used in this installation of only 120 m² offer excellent heat exchange capacity, despite their low refrigerant charge.
This project was carried out for our loyal customer Frigosystem with whom, over the years, we have had the good fortune to collaborate on very important plants, just like this one which, with its production of 60,000 jars of tomato pulp per hour, is one of the most important tomato processing plants in Europe.
The word to the costumer
“Once again, Stefani has proved to be the ideal partner to ensure significant energy savings for the end customer. Attention to requirements and the flexibility with which it adapts to projects make Stefani an indispensable partner!”.
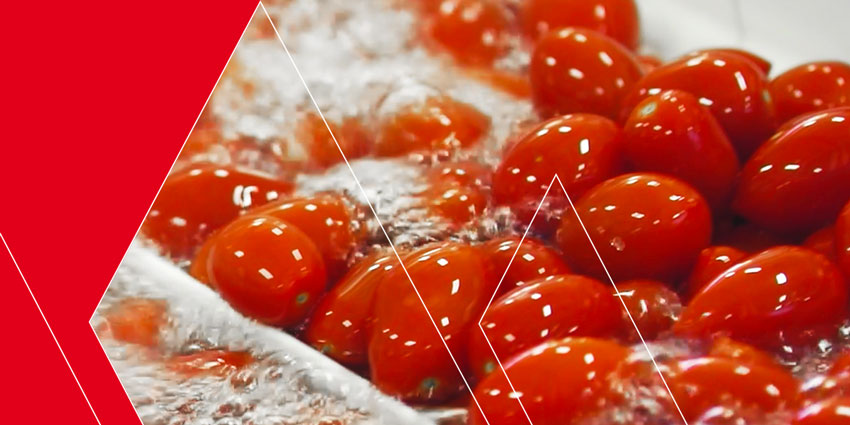
Emilia Romagna, Italy
Process cooling for a tomato processing plant
The end customer, one of Italy’s largest agri-food brands specialising in tomato processing, needs to cool the water from the tomato pulp pasteurisation process immediately after bottling in glass jars.
Storage description
This large plant is located near Cremona in the fertile Po Valley and includes all stages of tomato processing, from harvesting to bottling. The cooling of the pasteurisation process takes place in three consecutive phases: from 90 to 50°C, from 50 to 20°C and from 20 to 7°C. The technical solution – designed and implemented by Frigosystem and Termoidraulica Busi – is to include two powerful dry coolers, a remote condenser and a chiller in the cooling process. Stefani dry coolers operate in ‘free cooling’ in the first two phases, without the need for a chiller. In the last phase, however, the chiller comes into operation, disposing of the heat through the powerful Stefani remote condenser.
Storage informations
The plant produces 60,000 jars of tomato pulp per hour.
The cooling capacity used in process cooling is 3.0 MW in free cooling and 1.5 MW with the chiller.
Thanks to free cooling, the solution allows a 30% saving in electricity consumption.
Installed products
In the two free cooling phases: OSTRO dry coolers
A large exchange surface, in consideration of the size of the machines, and extremely powerful fans allow high-performance free cooling of the system.
In the cooling phase with the chiller: OSTRO remote condenser
The OSTRO XL series uses low refrigerant charge technology: less than 350 kg of gas for a 1500 kW condenser at DT 10K.
Advantage obtained
Thanks to the collaboration with our customer Frigosystem and Termoidraulica Busi, the end customer obtained a low energy solution, which also allows him to reduce water consumption. The OSTRO units used in this installation of only 120 m² offer excellent heat exchange capacity, despite their low refrigerant charge.
This project was carried out for our loyal customer Frigosystem with whom, over the years, we have had the good fortune to collaborate on very important plants, just like this one which, with its production of 60,000 jars of tomato pulp per hour, is one of the most important tomato processing plants in Europe.
The word to the costumer
“Once again, Stefani has proved to be the ideal partner to ensure significant energy savings for the end customer. Attention to requirements and the flexibility with which it adapts to projects make Stefani an indispensable partner!”.